The Role of Automotive Metal Fabrication
Automotive metal fabrication, a cornerstone in vehicle manufacturing, is an intricate process that shapes and strengthens the backbone of every vehicle. From sleek body panels to robust engine components, this technique is pivotal in crafting vehicles that are not only aesthetically appealing but also structurally sound and safe.
The Evolution of Metal Fabrication in the Automotive Industry
The journey of metal fabrication in the automotive industry is a tale of innovation and adaptation. In the early days, the focus was primarily on basic functionality, where rudimentary processes shaped the metal into fundamental vehicle components. However, as technology advanced, so did the techniques in metal fabrication. Today, the field is characterized by a synergy of advanced technologies and innovative materials, driven by an ever-increasing demand for efficiency, safety, and environmental sustainability.
Key Milestones in the Evolution:
- Early 20th Century: Basic metalworking techniques, largely manual;
- Mid-20th Century: Introduction of automated machinery, enhancing precision;
- Late 20th Century: Advent of computer-aided design (CAD) for more intricate parts;
- 21st Century: Integration of robotics and AI, pushing the limits of what can be fabricated.
Materials Matter: Exploring Metals Used in Automotive Fabrication
In the realm of automotive metal fabrication, the choice of material is pivotal. Each metal used in vehicle construction brings its unique set of properties, influencing the vehicle’s performance, safety, and longevity.
Common Metals and Their Uses:
- Steel: Predominantly used for chassis and frames due to its high strength and durability;
- Aluminum: Favored for body panels and engine components to enhance fuel efficiency, owing to its lightweight nature;
- Magnesium and Titanium: Occasionally used for specialized parts, offering a blend of lightness and strength.
Comparative Table of Metals:
Metal | Uses in Automotive | Benefits | Drawbacks |
---|---|---|---|
Steel | Chassis, Frames | Durable, strong | Heavier, prone to corrosion |
Aluminum | Body Panels | Lightweight, corrosion-resistant | Less strength than steel |
Magnesium | Engine Blocks | Ultra-lightweight, strong | Costly, flammable at high temperatures |
Titanium | Exhaust Systems | High strength-to-weight ratio | Very expensive |
Cutting-Edge Techniques in Metal Shaping and Molding
Modern automotive metal fabrication leverages a myriad of techniques to shape and mold metals with precision and complexity. These methods have been refined over years, allowing manufacturers to produce parts that are robust yet lightweight.
Key Techniques:
- Stamping: Used for creating body panels and complex shapes;
- Welding: Essential for joining different metal parts securely;
- Laser Cutting: Offers unparalleled precision in cutting metal sheets.
The Impact of Automation and Robotics in Metal Fabrication
Automation and robotics have revolutionized the field of automotive metal fabrication, heralding a new era of manufacturing efficiency and precision. The introduction of robots in the manufacturing process has been a game-changer, ensuring consistent quality across production lines. These technological marvels are known for their precision and efficiency, dramatically enhancing the speed of production while also playing a pivotal role in reducing operational costs. The consistency and precision brought by robotics have elevated the standards of quality in automotive metal fabrication. Additionally, the automation of many processes has enhanced safety within the industry by reducing human involvement in hazardous tasks, thereby minimizing the risk of accidents. Another significant benefit of automation is cost efficiency. The use of robots and automated systems has led to reduced labor costs and increased throughput, optimizing the overall manufacturing process and delivering economies of scale.
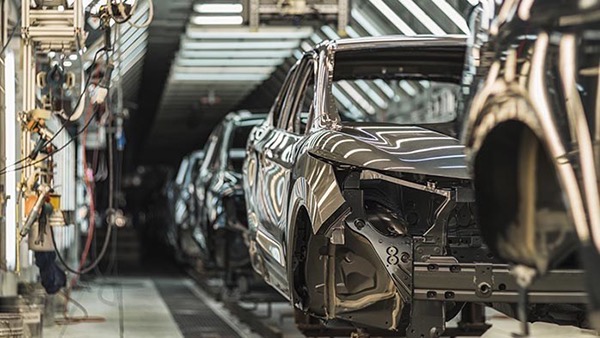
Customization and Personalization through Metal Fabrication
Automotive metal fabrication has significantly expanded the scope for customization and personalization in vehicle manufacturing. This aspect of fabrication caters to the diverse preferences and requirements of consumers, allowing for a range of personalization options. Vehicles can now be tailored to individual tastes, from the exterior design to the vehicle’s internal layout. Personalized body shaping allows customers to have a say in the external design of their vehicles, making each car unique to its owner. Structural modifications are another aspect of customization, enabling changes to the vehicle’s internal layout to meet specific needs or preferences. Additionally, the option for unique color schemes provides an added layer of individuality, allowing consumers to choose custom colors that reflect their personality or style.
Crankshaft Design in Automotive Metal Fabrication
The crankshaft is a fundamental component in the automotive engine, playing a critical role in converting the linear motion of pistons into rotational motion. In the context of automotive metal fabrication, the design and manufacturing of crankshafts represent a blend of precision engineering and material science. The evolution of crankshaft design is closely linked with advancements in metal fabrication techniques, showcasing how changes in one aspect of automotive engineering can ripple through to others.
Key Aspects of Crankshaft Design:
- Material Selection: The choice of material for crankshafts is crucial. High-strength steel alloys are commonly used for their balance of strength, durability, and cost-effectiveness. The material must withstand significant stress and wear over prolonged periods, making the selection process a key aspect of crankshaft design;
- Fabrication Techniques: Modern fabrication methods such as forging and precision machining are employed to create crankshafts. Forging ensures the strength of the metal, while machining provides the necessary precision for the crankshaft to function effectively;
- Balancing and Weight Considerations: A well-balanced crankshaft is essential for the smooth operation of the engine. The design process involves careful consideration of the crankshaft’s weight and distribution to minimize vibrations and ensure efficient power transfer;
- Heat Treatment Processes: To enhance the durability and wear resistance of crankshafts, various heat treatment processes are used. These processes alter the microstructure of the metal, improving its properties to suit the demanding environment of an automotive engine.
The design and fabrication of crankshafts exemplify the intricate relationship between component design and metal fabrication in the automotive industry. As metal fabrication techniques continue to evolve, they open up new possibilities for enhancing the performance and efficiency of essential components like crankshafts. The future of automotive metal fabrication, with its focus on advanced materials and precision engineering, is likely to bring further innovations in crankshaft design, contributing to more efficient and powerful engines.
Conclusion
Automotive metal fabrication remains an essential and evolving aspect of vehicle manufacturing. As technologies advance and consumer demands shift, this field will continue to shape the very essence of our vehicles, making them safer, more efficient, and more aligned with the needs of a changing world.
Leave a Reply