Exploring Innovations in Headlight Design
The automobile industry exhibits intense competition. Approximately 30% of all cars globally are produced in China, and 10% in Japan. Annually, the world produces about 72 million automobiles. Considering this, the number of different designs created each year is substantial, likely reaching into the thousands. Each automobile typically includes at least two lights, with many featuring additional lamps on the rear windshield. Consumer preferences often prioritize design in vehicle selection, with lamps significantly influencing a vehicle’s image. Investing time and money in designing superior car lamps is a strategic decision.
The article provides detailed insights into the primary steps necessary for designing and manufacturing light guides for automotive headlights.
Understanding Light Guides
- Light guides are unique components, often in the form of special tubes manufactured from PMMA (acrylic glass) or polycarbonate;
- The primary advantage of these guides is their light transmission capability, where a light source on one end can illuminate the entire length of the tube;
- These properties enable the creation of complex and visually stunning lighting effects in automotive headlights.
Designing Light Guides
The design process of a light guide involves determining the trajectory of the tube and selecting its external and internal diameters. The primary aim of most light guide designs is to accentuate the contours of the lamp. This is achieved by shaping the tube into the desired form and integrating LED diodes. These diodes are either positioned at one end of the tube at an angle between 30 and 45 degrees or distributed as numerous smaller diodes along the entire length of the tube.
Light tubes are subject to specific performance standards, including a minimum light transmission efficiency of 50%. Achieving this requires the light guide to be a completely clear component, free from any bubbles or structural irregularities that could cause light distortion. To reflect and transmit light effectively, the tube’s surface must be exceptionally smooth, often finished to a surface roughness of up to Ra 0.32 microns.
Casting: The First Step to a Functional Prototype
PMMA excels in casting and injection molding applications. While injection molding is ideal for large-scale production, its tooling costs can be prohibitively expensive for smaller batches. Consequently, urethane casting has become the most popular method for creating PMMA prototypes. This approach is more cost-effective, utilizing silicone instead of steel for the mold, and a single mold can produce between 12 to 20 parts.
The quality of the final part’s surface finish is directly influenced by the master model’s quality. This model can be created either through machining or 3D printing, followed by post-processing to achieve the desired quality. It’s important to note that when undertaking the casting process independently, it is advisable to source the master model from a specialized prototyping machine shop. Such shops can produce superior master models, resulting in higher quality cast parts and reducing the need for extensive machining post-casting.
Enhancing Quality Through Preliminary Machining
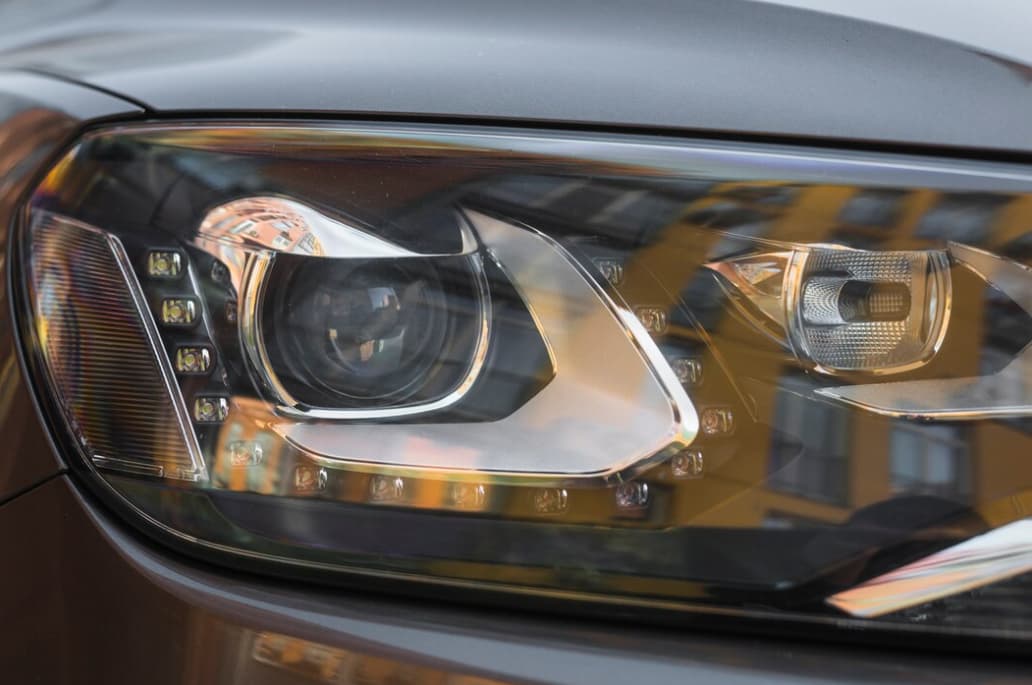
After casting the component, it’s important to recognize that manufacturing techniques involving melting and solidification of material typically lack high precision, and the surface finish of the part may not yet match the quality of glass. Therefore, machining is frequently the subsequent step in fabricating a precise light guide. Achieving a clear and accurate part necessitates multiple processing stages. The initial phase is preliminary machining, which involves creating mounting holes and shaping secondary surfaces.
Achieving Perfection: Finishing Operations
Completing the light guide is the most challenging phase of the process. Any errors at this stage often necessitate starting from scratch and remaking the part entirely.
- This final stage typically involves precise 5-axis milling;
- A slender, pointed diamond tool is then used to refine the PMMA into a glass-like finish;
- To ensure maximum surface uniformity, the part undergoes polishing;
- This process typically starts with 400 to 600 grit sandpaper, adjusted based on the initial quality of the part, and concludes with 1500-2000 grit, using a special polishing paste.
The end product is a transparent, clear surface with optical prototyping qualities akin to simple glass, yet it boasts greater tensile strength and lower brittleness. This enhanced durability allows the light guide to withstand significant impacts.
The Importance of Testing in Light Guide Production
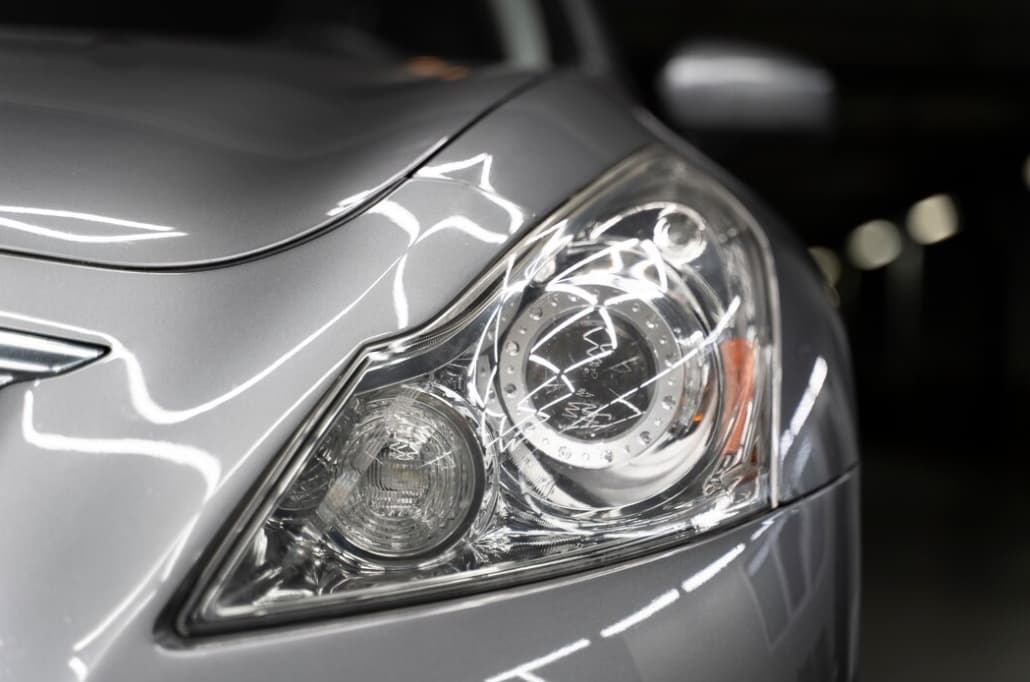
Testing is a vital component in the production of light guides. Photometry, a method to measure light’s intensity as perceived by the human eye, is primarily used. A conventional testing setup comprises a lamp prototype on a rotating platform, a screen to focus on specific light areas, and a photometer to measure light intensity. Adjustments to the lighting source can rectify any deficiency in light intensity without requiring substantial design modifications.
Light guides are more than just decorative elements in a car’s design. They play a pivotal role in improving road safety by enhancing the visibility of the vehicle and providing better illumination. Through complex designs and strategic placement of LED diodes, light guides optimize light distribution, reduce glare for oncoming traffic, and improve the driver’s visibility, especially during night times and adverse weather conditions.
As sustainability becomes a major consideration in automotive design, light guides play a part in reducing the environmental impact. By making use of LED technology, light guides are energy efficient, reducing power consumption. Plus, their long lifespan reduces the need for frequent replacements, contributing to waste reduction.
Conclusion
Mastering the art of creating light guides is a complex yet rewarding process for the automotive industry. It combines precision engineering with artistic creativity, resulting in designs that are not only visually stunning, but also enhance road safety and decrease environmental impact. With continuous advancements in technology and growing emphasis on sustainability, the journey toward perfecting headlight designs is an evolving pursuit of excellence.
The process of designing and manufacturing light guides for car headlights is both complex and fascinating, blending artistry with precision engineering. These clear plastic prototypes, created through a meticulous series of steps from casting to final finishing, play an influential role in shaping a vehicle’s aesthetic appeal and safety. As technology evolves and sustainability becomes more significant, the way forward for headlight design lies in continuous innovation, enhanced safety functionality and environmental consciousness. All these factors make the production of light guides an intriguing journey in the pursuit of automotive excellence.
Leave a Reply