Motorparts Design: Engineering for Peak Performance
In the dynamic world of automotive manufacturing, the choice of materials for motor parts plays a pivotal role in defining the performance, durability, and efficiency of vehicles. This comprehensive exploration delves into the various metals used in auto parts manufacturing, examining their unique properties, applications, advantages, and the emerging trends that are shaping the future of automotive design.
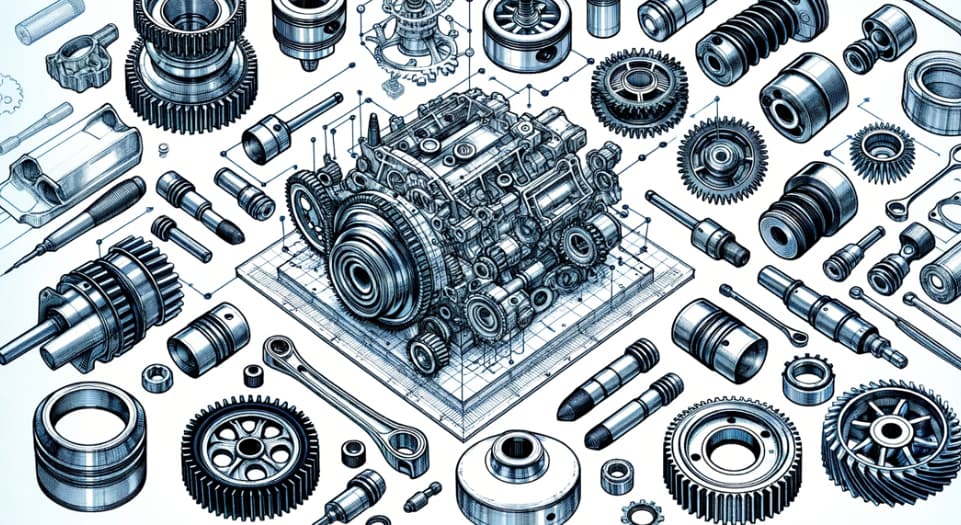
Metals have been the cornerstone of automotive manufacturing due to their robustness, durability, and cost-effectiveness. These materials have not only facilitated the mass production of car components but have also guaranteed reliability and longevity. Metals like aluminum, steel, titanium, iron, magnesium, and copper, each with distinct properties, have been instrumental in automotive innovation.
Benefits of Metal Materials in Car Parts
The use of metal in car parts comes with numerous advantages. Their ease of maintenance, stemming from their excellent heat conduction, makes them vital in keeping engine electronics cool and functioning optimally. Additionally, metals are resistant to damage from automotive fluids, ensuring longevity with minimal maintenance.
Metal’s versatility in forming complex shapes has made it indispensable for intricate car components like fuel systems, brakes, and suspensions. The strength and lightweight nature of certain metals, particularly aluminum and titanium, contribute to vehicle safety and fuel efficiency.
Common Metals in Auto Parts Manufacturing
1. Aluminum: The Versatile Metal
Aluminum is renowned for its lightweight and corrosion-resistant properties. Its use spans across various auto parts, including engine blocks, wheels, transmission housings, body panels, and interior trims. Aluminum’s versatility extends to automotive lighting systems as reflectors and heat shields. The most common form of aluminum in auto manufacturing is alloys, which are combinations of aluminum with other metals, tailored to achieve specific properties for different auto parts.
2. Steel: The Foundation of Strength
Steel, known for its strength and moldability, is widely used in the automotive industry. The variety of steel types, including 9- and 10-carbon steel alloys, cater to different automotive needs. The selection of a specific type and grade of steel enables engineers to create parts with precise properties needed for each application, from body panels to advanced safety features.
3. Titanium: The High-Performance Metal
Titanium, with its excellent strength-to-weight ratio and corrosion resistance, is primarily used in high-performance parts like brake rotors and wheels. Its unique properties are especially beneficial in racing vehicles, enhancing fuel economy and reducing emissions.
4. Iron: The Economical Choice
Iron’s affordability and ease of manipulation make it a popular choice in automotive manufacturing. It’s widely used for various car parts, including frames, axles, and engine components. Iron alloys, created by combining iron with other metals, offer enhanced properties such as improved strength and corrosion resistance.
5. Magnesium: The Innovator in Lightweight Design
Magnesium, known for its strength and lightweight, is used in high-end sports cars to reduce overall vehicle weight while maintaining durability. Its ability to be cast into complex shapes makes it ideal for creating custom automotive components, despite its higher cost and fabrication challenges.
6. Copper: The Conductor of Choice
Copper’s excellent electrical conductivity makes it ideal for automotive electrical components and engine cooling systems. Copper-based alloys, enhanced with other metals, provide additional strength and corrosion resistance, making them suitable for applications like exhaust systems and brake pads.
The Future of Metal Automotive Parts: Lightweight and Efficient
The automotive industry is increasingly focusing on lightweight metal parts to improve fuel efficiency and reduce emissions. The use of lightweight metals like aluminum and magnesium, along with composite materials, is becoming more prevalent. This trend is especially significant in electric vehicle manufacturing, where reducing vehicle weight can greatly enhance range and performance.
Composite materials, combining various fibers like carbon, glass, and Kevlar®, offer a balance of light weight, strength, and thermal properties. These advanced materials are set to play a crucial role in future automotive part design, marking a shift from traditional metals to more sophisticated, multifaceted composites.
Advantages and Disadvantages of Common Metals in Auto Manufacturing
Each metal used in automotive manufacturing comes with its set of advantages and disadvantages, influencing their application in different car parts.
- Aluminum: Lightweight but Costly. While aluminum offers the advantage of being lightweight and corrosion-resistant, it can be more expensive than other metals like steel. Its manufacturing process may also require specialized equipment and techniques;
- Steel: Durable but Heavy. Steel is celebrated for its durability and ease of manufacturing. However, its heavier weight compared to aluminum or magnesium can impact fuel efficiency. Innovations in steel manufacturing are focusing on creating lighter and stronger steel alloys to overcome this limitation;
- Titanium: Strong but Challenging to Work With. Titanium is exceptionally strong and lightweight but is more challenging to process than other metals. Its high cost and manufacturing complexity limit its use to high-performance or luxury vehicles;
- Iron: Affordable but Prone to Corrosion. Iron is cost-effective and easy to work with but is more prone to corrosion than other metals. Iron alloys have been developed to improve corrosion resistance and strength, making them more suitable for various automotive applications;
- Magnesium: Innovative but Difficult to Fabricate. Magnesium is innovative in creating lightweight parts but is difficult to fabricate and more expensive than traditional metals like steel and iron. Its use is often limited to high-end or performance-focused vehicles;
- Copper: Conductive but Expensive. Copper is an excellent conductor of electricity and heat, making it ideal for specific automotive applications. However, its cost and weight can be higher than other metals, limiting its use to specific components where its properties are most beneficial.
Technological Advancements in Metal Manufacturing
The continual advancement in metal manufacturing technologies is reshaping the automotive industry. Innovations in metallurgy and fabrication techniques are enabling the creation of stronger, lighter, and more cost-effective metal parts. These advancements are not only improving the performance and efficiency of vehicles but also reducing their environmental impact.
New technologies like additive manufacturing (3D printing) are revolutionizing how metal parts are produced, allowing for more complex designs and rapid prototyping. This technology enables the creation of parts that were previously impossible or too expensive to manufacture using traditional methods.
Environmental Impact and Sustainability
The automotive industry’s shift towards more sustainable and environmentally friendly practices is influencing the choice of materials for motor parts. The recyclability of metals like aluminum and steel is a significant advantage, contributing to the industry’s sustainability efforts. Additionally, the use of lighter metals and composites in vehicle manufacturing is reducing carbon emissions, aligning with global environmental goals.
Conclusion
The evolution of metals in motorparts design reflects the automotive industry’s commitment to innovation, efficiency, and environmental responsibility. From the robustness of steel and iron to the lightweight properties of aluminum and magnesium, each metal has uniquely contributed to automotive advancements. As the industry moves towards a future dominated by electric vehicles and a focus on sustainability, the role of these metals, alongside emerging composites, will continue to be pivotal in shaping the cars of tomorrow. The ongoing technological advancements in metal manufacturing and the industry’s shift towards lighter, more efficient materials are set to redefine automotive design and performance in the years ahead.
Leave a Reply