EV Battery Box Design: How To Make It A Reality
The electric vehicle (EV) market is rapidly evolving, with advancements in technology driving it forward. Central to these innovations is the EV battery box – a critical component that houses and protects the vehicle’s power source. This article delves into the intricacies of EV battery box design, exploring how to transform these concepts into tangible realities.
Understanding the Core of EV Technology: The Battery Box
The battery box in an electric vehicle (EV) is more than just a protective case; it’s the linchpin of the vehicle’s power system. It must be robust to protect against physical impacts, lightweight to not excessively burden the vehicle, and efficient to not hamper the vehicle’s performance. These requirements have led to innovative designs and material choices. For instance, the integration of shock-absorbent structures within the box enhances safety without significantly increasing weight. Additionally, the design often incorporates features for easy maintenance and battery replacement, ensuring the box is not just a shield, but a functional component of the EV’s architecture.
The Intersection of Design and Material Choice
When it comes to the material selection for a battery box, the choice is a delicate balance between strength, weight, and durability. Commonly used materials include:
- Carbon Fiber Composites: Known for their high strength-to-weight ratio and durability. They are resistant to corrosion and have excellent thermal properties;
- Aluminum Alloys: Popular for their light weight, good thermal conductivity, and cost-effectiveness. However, they may not be as strong as carbon fiber composites.
Material | Strength | Weight | Durability | Thermal Conductivity |
---|---|---|---|---|
Carbon Fiber | High | Low | High | Moderate |
Aluminum Alloys | Moderate | Low | Moderate | High |
Each material has its own set of advantages and limitations, making the choice heavily dependent on the specific requirements of the EV design.
Innovations in Thermal Management Systems
Thermal management is a pivotal aspect of battery box design, ensuring that batteries operate within their optimal temperature range. This is crucial for maintaining battery efficiency, longevity, and safety. Innovations in this area include:
- Active Cooling Systems: Utilizing coolants to actively regulate battery temperature;
- Passive Cooling Systems: Relying on heat sinks and thermal pads to dissipate heat naturally.
These systems are often combined with smart sensors to monitor temperatures and adjust cooling mechanisms accordingly.
Balancing Safety and Efficiency: A Designer’s Dilemma
Safety is the foremost priority in EV battery box design. Designers aim to create a box that can withstand high-impact scenarios, protecting the battery from damage. This involves using crumple zones and reinforced structures. However, there’s a balance to be struck between safety and efficiency. The box should not be so heavy that it significantly reduces the vehicle’s range or performance. Advanced computational methods are often employed to simulate different scenarios, ensuring the design is both safe and efficient.
The Role of Modularity in EV Battery Design
Modularity in battery box design allows for greater flexibility and adaptability. Modular designs can accommodate various battery sizes and types, making them suitable for different vehicle models. This approach also simplifies the manufacturing process and allows for easier upgrades or replacements of battery units.
The Impact of Aerodynamics on Battery Box Design
Aerodynamics significantly affects an EV’s efficiency. The design of the battery box can influence the overall aerodynamic profile of the vehicle. Sleek, streamlined designs help reduce drag, thereby improving range and performance. Computational fluid dynamics (CFD) software is often used to model and optimize the aerodynamic efficiency of battery box designs.
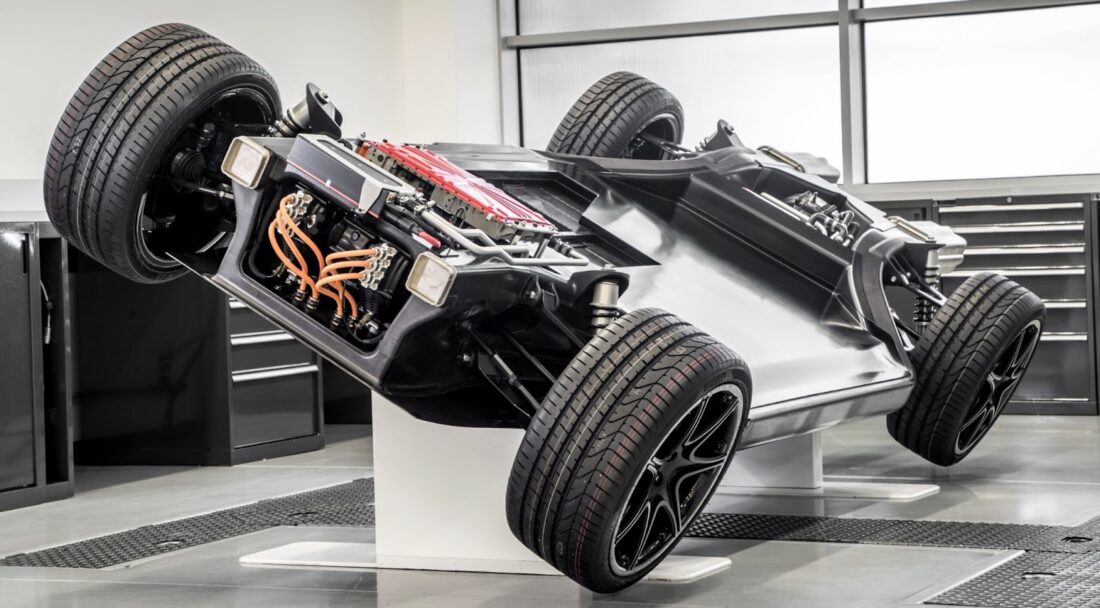
Leveraging Technology: Software in Battery Box Design
Software plays a transformative role in the design of battery boxes. Simulation and modeling software enable designers to predict how designs will perform under various conditions. This includes stress testing, thermal performance modeling, and impact simulation. Such tools allow for the rapid iteration of designs, ensuring that the final product is both safe and efficient.
From Concept to Reality: The Manufacturing Process
The manufacturing process for EV battery boxes involves several steps:
- Design and Prototyping: Initial concepts are developed and refined using CAD software;
- Material Selection: Based on the design requirements, appropriate materials are chosen;
- Manufacturing: Techniques like injection molding, CNC machining, or composite layup are used to create the components;
- Assembly: Components are assembled, often including the integration of cooling systems and electronic controls;
- Testing: The final product is rigorously tested for safety, durability, and performance.
Navigating Regulatory Standards and Certifications
Compliance with regulatory standards and certifications is essential in battery box design. These standards ensure that the battery boxes meet safety, environmental, and performance benchmarks. Key standards include ISO, SAE, and various national and regional regulations. Designers must stay abreast of these evolving standards to ensure compliance.
The Future is Electric: Emerging Trends in EV Battery Box Design
Emerging trends in EV battery box design include:
- Integration of Smart Technologies: Incorporating sensors and IoT connectivity for real-time monitoring and diagnostics;
- Use of Eco-Friendly Materials: Exploring sustainable materials that reduce environmental impact without compromising performance;
- Advanced Manufacturing Techniques: Utilizing 3D printing and other novel manufacturing methods to create more complex and optimized designs.
Conclusion
The journey from conceptualizing to actualizing an EV battery box design is filled with challenges and opportunities. Innovations in materials, thermal management, and software are propelling the industry forward, paving the way for safer, more efficient, and more sustainable electric vehicles.
Leave a Reply