Unraveling the Future of Automotive Product Design
Product development holds a central role in various industries, notably within automotive product design. In this sector, product development processes have evolved significantly to address the needs for innovation, creativity, and industry-specific demands. This evolution resembles the transition from prototype to production, with the inclusion of ideation and market entry into the workflow.
Successfully bringing a new item to market can be challenging when manufacturers do not fully understand the intricacies involved in its development. Therefore, this conversation aims to clarify the steps and best practices in developing new automotive items, shedding light on the entire process specifically for the automotive sector. In the realm of automotive product design, automotive lighting design emerges as a pivotal element, influencing both aesthetics and functionality in shaping the overall design and safety features of modern vehicles.
Exploring the Product Development Process
The product development process encompasses a series of stages that trace a product’s journey from initial idea to its final introduction to the consumer. This comprehensive concept covers the phases of new product ideation, design, production, quality checks, introduction, and market debut.
Specifically in the automotive sector, product development plays a crucial role in automotive design, influencing each new feature and addition in a vehicle. Moreover, for companies adopting an innovative approach, a thorough understanding of the product development cycle can facilitate a more seamless entry into the market.
Understanding the Vital Role of Product Development
Product development stands as a pivotal element in the pursuit of business success. Here’s an exploration of why understanding and executing effective product development is vital:
- Enhancement of Product Quality: A well-executed product development process is crucial for maintaining quality assurance and control in manufacturing. Adhering rigorously to a product development plan enables manufacturers to elevate their product quality, ensuring that it meets their high standards. This quality improvement is a result of investing in robust research, thoughtful design, precise engineering, and meticulous inspection. Such investments lead to the creation of products that are not only durable and efficient but also reliable. This reduction in product defects and recalls strengthens consumer trust and heightens customer satisfaction;
- Reduction in Costs: A comprehensive product development process, crafted by experts across various production stages, allows for the optimization of product design. This optimization ensures that the product is not only effective but also easier to manufacture. Moreover, it opens avenues for reducing material costs, discovering more efficient manufacturing processes, and minimizing material waste. Such strategic planning in product development not only enhances the quality and effectiveness of the final product but also significantly lowers production costs, contributing to the overall efficiency and profitability of the business;
- Fostering Innovation and Unique Features: The heart of product development lies in innovation and differentiation, which are crucial across various industries. Achieving innovation is feasible through significant investment in a robust research and development department. This investment leads to the creation of unique, value-added, and technologically advanced components in the automotive field. The benefits of dedicating considerable time and resources to product differentiation are numerous, including market distinction, enhanced quality, and the attraction of both new and returning customers;
- Enhancing Collaboration and Customer Involvement: Beyond the manufacturing aspect, the product development process is greatly influenced by customer feedback. Engaging customers in this process is essential. Engaging with customers provides valuable insights into their needs, challenges, and their perspectives on potential solutions. While not all customer feedback may be directly implemented, adopting a collaborative approach can significantly enhance customer relationships, fostering loyalty and trust. This customer-centric strategy in product development ensures that the end product aligns more closely with consumer expectations and needs.
Exploring the Seven Phases of the Product Development Cycle
The product development process encompasses seven distinct stages, each critical for the successful creation and introduction of a product. Here’s a detailed explanation of these stages and key aspects to consider:
Generation of Ideas
The inception of any product begins with the generation of an idea. This encompasses the various features, its functionality, and aesthetic elements. While brainstorming is a common method for idea generation, a more effective strategy involves conducting market research and incorporating customer feedback, especially for optimizing the design and usability.
Evaluation and Screening
Following the generation of ideas, these concepts are subjected to thorough evaluation and screening. This step assesses the feasibility of manufacturing and market entry. It’s a demanding process, as the idea must align with the company’s goals and resources. Factors such as market potential, profitability, and customer acceptance are crucial in this phase. Ideas that fail to pass this evaluation are discarded.
Development of Concept
At this stage, manufacturers develop a detailed design outlining the product’s functions, features, and target market. This step allows for the gathering of organic customer feedback and further validation of the concept. Although a prototype is not yet produced, the product design should be fully conceptualized.
Design and Prototyping
The intensive work of design and prototyping takes place in this phase. Once the product design is established, prototyping begins to test and refine the product. This includes evaluating both functionality and aesthetics, particularly if aesthetics influence function. Common methods for prototyping are 3D printing and CNC prototype machining. The prototyping phase involves continuous optimization until the product meets the desired standards.
Testing and Validation
The prototype undergoes extensive testing and validation to ensure optimal performance. Tests typically include safety, usability, and functional evaluations. In the automotive industry, compliance with all relevant automotive part regulations is also assessed.
Manufacturing and Production
With the product tested and validated, manufacturing commences. It’s essential that this process remains consistent and does not compromise the product’s quality. Manufacturing techniques vary, including injection molding, CNC machining, sheet metal fabrication, and die casting. The choice of method depends on the type and materials. For instance, automotive product design might use insert molding for mixed plastic and metal parts, or over-molding for separate but connected plastic components. The selection is tailored to the specific requirements of the project.
Launch
The final step in automotive product development is the market introduction of the product. Pre-launch preparations involve developing effective marketing strategies, establishing supply chain and distribution channels, and officially launching the product. Product development does not cease post-launch; feedback from users is crucial for ongoing improvements and refinements.
Steps in Automotive Product Development
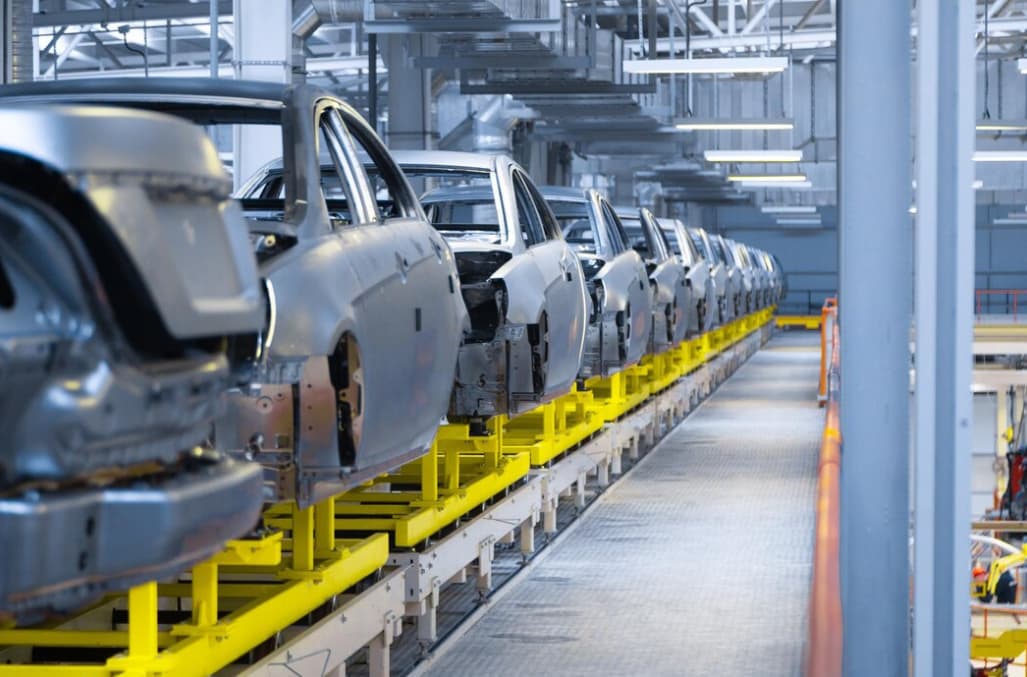
The creation of third-party automotive parts often involves examining the current automotive industry landscape and identifying components that can be enhanced in terms of functionality, and occasionally in aesthetics or ergonomics. Consider the development of an automotive lighting component, such as a headlight, as an illustrative example. This process necessitates cooperation among designers, engineers, suppliers, and regulatory bodies. The following outlines the stages of development in the automotive industry, using headlights as a case study.
Market Research and Analysis
The initial step involves analyzing the market for various headlight types, their designs, and the range of vehicles they cater to, from general cars to high-end models. High aesthetics are particularly significant in the latter category. Subsequent steps include assessing the competition and identifying any gaps in their offerings. The goal is to ensure that the new product not only matches but also surpasses competitors by addressing these gaps.
Concept Development
Based on the available materials and other factors, generate concepts for the proposed headlight. These could focus on aspects like efficiency, aesthetics, longevity, or functionality. Create clear sketches for visualizing the design and its integration into vehicles.
Design and Engineering
Transform the sketches into CAD models and work with engineers to finalize the headlight’s placement and performance characteristics. This stage might also explore the use of advanced lighting technologies. The engineering analysis should confirm compliance with all required standards.
Prototyping and Testing
Construct a prototype using methods like 3D printing or CNC machining. Test the prototype for brightness, beam pattern, and durability, and make optimizations based on the feedback. Each step should adhere to strict quality control measures and meet safety and regulatory standards, such as specified brightness levels and beam patterns.
Developing a Manufacturing Plan
Formulate a plan for mass-producing the lighting system. Options vary based on business size and include purchasing manufacturing systems and machines or outsourcing to service providers. Source necessary components and materials from suppliers.
Marketing and Launching
Devise a launch strategy and marketing campaign to inform target audiences about the new product. After launching, gather customer feedback on performance and other features, and use this input for ongoing product improvements.
Best Practices in Industrial Product Development
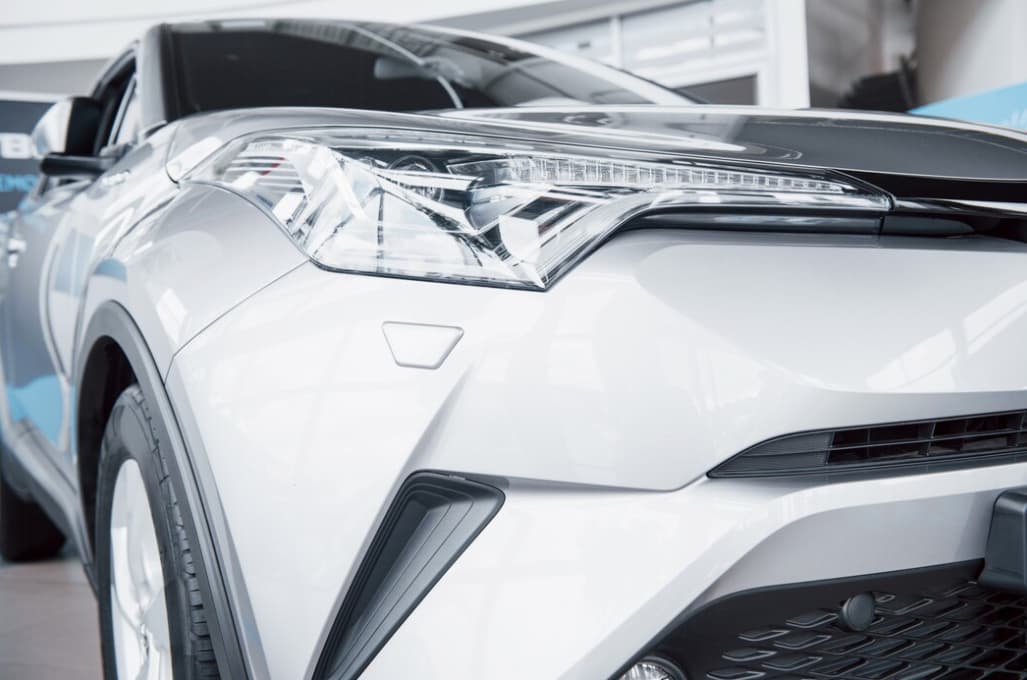
Industrial product development, particularly in the automotive sector, presents unique challenges and opportunities. This field demands staying ahead of market trends, prioritizing innovation, and ensuring safety. Here are some strategies and best practices for effective industrial product development, with a focus on automotive manufacturing:
- Leveraging Cutting-Edge Technology: Incorporate the latest technologies to accelerate production cycles while maintaining high quality. This often involves substantial initial investment in advanced machinery. An alternative approach for those with limited capital is to partner with service providers who offer access to these technologies. This strategy enables smaller manufacturers to compete effectively in the market;
- Adherence to Regulatory Standards: The automotive industry is heavily regulated to ensure safety and reliability. It is crucial to stay informed about industry regulations, requirements, and standards. Products must meet all certification and compliance criteria to avoid legal and regulatory complications;
- Rigorous Prototyping and Testing: A thorough testing phase is essential to confirm the functionality and safety of the product. Utilizing appropriate simulation techniques and tests helps identify and address issues early in the development process. Continual refinement and retesting of prototypes, although time-consuming, can significantly reduce the risk of product recalls due to defects;
- Selecting Dependable Suppliers: The quality of suppliers directly impacts the success of the product. Selecting reliable suppliers for components and raw materials is critical. Evaluating a supplier’s track record can provide insights into their reliability and commitment to quality. A strong supplier partnership is fundamental to maintaining a smooth and quality-centric supply chain.
Conclusion
In the automotive sector, the development of new offerings plays a pivotal role in driving success. This process empowers manufacturers to elevate quality, reduce expenses, encourage innovation, comply with regulations, strengthen teamwork, optimize supply chains, and keep pace with market trends. Automotive firms investing in this area are well-positioned to deliver superior offerings, satisfy customer needs, and secure a competitive advantage in a rapidly changing industry.
For those seeking a dependable partner for automotive product development, WayKen stands as an excellent choice. As a comprehensive prototyping and manufacturing service provider, WayKen specializes in CNC machining, 3D printing, and injection molding. Boasting 20 years of expertise in automotive prototyping and part production, WayKen delivers cost-effective machining solutions tailored to each car prototype and part. To embark on a new project, reaching out to WayKen is a promising start.
FAQ
This depends on the complexity, regulations, and the business’s internal process. It can range from a few months to several years. Some projects even take longer.
Prototyping is critical in automotive product development because it helps assess product functions and aesthetics. Hence, it is possible to identify any design flaws and make necessary improvements. It also helps in meeting the quality standard.
This is important as it aids the supply of quality materials, components, and subsystems which can help reduce defects. Also, it helps in cost efficiency and reduces lead times of such products.
Leave a Reply